Filtration von Hydraulikflüssigkeiten
Höhere Drücke auszuhalten, größere Volumen zu fördern und länger im Einsatz zu sein, sind nur einige der Anforderungen, denen sich Hydrauliksysteme heutzutage stellen müssen, und die eine nachhaltige Filtration und regelmäßige Überprüfung durch Ölanalysen unerlässlich machen. Denn Voraussetzung für den störungsfreien, zuverlässigen Betrieb einer Hydraulikanlage ist saubere Hydraulikflüssigkeit. Wird diese nicht ausreichend gewartet und gepflegt, kommt es zu vorzeitiger Alterung und Additivabbau.
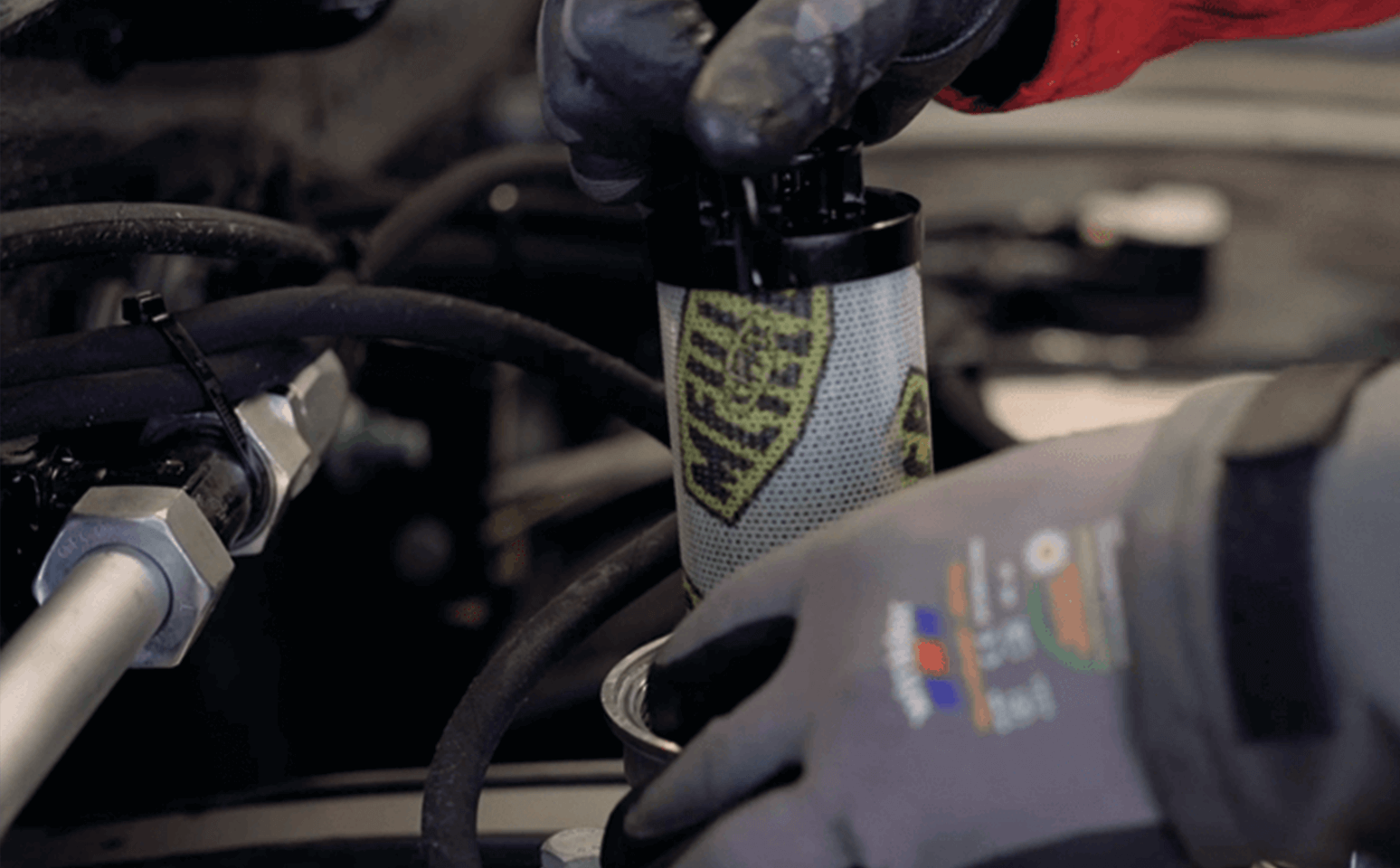
Reduzierte Schmierfähigkeit beschleunigt wiederum den Verschleiß der Komponenten im Hydrauliksystem. Kontaminierte Hydraulikflüssigkeiten verursachen so ungeplante Maschinenausfälle, Stillstandzeiten und erhöhte Lifecycle-Kosten bei der Nutzung der Maschinen. Hier helfen die in der Filtertechnik eingesetzten Verschmutzungsanzeigen - egal, ob optisch oder elektronisch. Sie zeigen den Bedienern nicht nur an, wann eine Wartung oder ein Filterwechsel vorzunehmen ist, sondern sind auch gemäß Maschinenrichtlinie DIN EN ISO 4413 gesetzlich gefordert. winkler als Spezialist für mobile Anwendungen hat ein reichhaltiges Lagerprogramm an namhaften Markenherstellern in den Bereichen „Filter“, „Condition Monitoring“* und auch „Ölanalyse“.
Verschmutzungsarten
Es gibt viele Arten der Verschmutzung von Hydraulikflüssigkeiten. So kann selbst Wasser im Öl zu Bakterien-, Pilz- und Hefebefall führen, und die Vermischung unterschiedlicher Druckflüssigkeiten oder Schmiermittel die Hydraulikflüssigkeit zersetzen. Eine weitere Gefahr sind Initialverschmutzungen. Sie entstehen, wenn Fertigungsrückstände und Konservierungsstoffe in den Komponenten (Pumpe, Ventil, Zylinder, etc.) zurückbleiben, oder wenn bei der Montage der Bauteile Schweißperlen, Metallspäne, Lackpartikel oder Staub in die Flüssigkeit gelangen. Selbst neu einzufüllende Hydraulikflüssigkeiten, die nicht der Reinheitsklassifikation der Komponentenhersteller entsprechen, stellen eine Gefahr dar. Dies gilt insbesondere bei Hydraulikflüssigkeiten, die in Tanks oder Fässern nicht fachgerecht gelagert werden. Durch natürliche Alterung der Druckflüssigkeiten werden wichtige Additive zerstört, die dann das gesamte System schädigen können.
Systemschmutz entsteht durch die mechanische Abnutzung der hydraulischen Bauteile in der Anlage selbst. Häufig sind bei Systemstart (Kaltstart) nicht alle beweglichen Bauteile und Hohlräume mit Hydraulikflüssigkeit geflutet. Durch die Haftreibung der hydraulischen Komponenten werden metallische Späne oder Rostpartikel abgelöst. Es können aber auch anorganische Fasern und Dichtungsabrieb freigesetzt werden und als natürliche Verschmutzungspartikel den Verschleiß der Komponenten beschleunigen und dadurch zu einem vorzeitigen Altern der Druckflüssigkeit führen.
Speziell für mobilhydraulische Arbeitsmaschinen und Geräte wie Baumaschinen oder Maschinen für den Agrar- und Forstbereich ist Umgebungsschmutz die größte Gefahr. Sie kontaminieren von außerhalb über Tankbelüftungen, beschädigte Dichtungen und/ oder Kolbenstangen an Hydraulikzylindern und Motoren das System. Auch bei Reparatur- und Wartungsarbeiten, die im Freien durchgeführt werden, gelangt meist Schmutz von außen in die Hydraulikanlagen.
Verschleiß reduzieren
Um den Verschleiß der hydraulischen Komponenten zu reduzieren, machen Systemhersteller für den sicheren Betrieb konkrete Angaben zur Reinheitsklassifikation gemäß ISO 4406. Die Festlegung der Reinheitsklasse nach dieser Norm verfolgt das Ziel, die vorhandenen Partikel pro 100 ml Druckflüssigkeit nach Größe und Anzahl zu klassifizieren. Gemäß ISO 4406 werden die Schmutzpartikelgrößen 4µm, 6µm, 14µm** zugrunde gelegt. Das Ergebnis wird mit Hilfe von Tabellen (s. Abb.) in dreistelligen Zahlenkombinationen ausgegeben, anhand derer der Verschmutzungsgrad (z.B. 18/16/13) der verwendeten Druckflüssigkeit nachgewiesen beziehungsweise bei Neugeräten vorgegeben werden kann.
Ölanalyse
Anzahl und Größe der Partikel im Öl werden gemessen, indem man eine Rasterscheibe mit der kontaminierten Hydraulikflüssigkeit bestreicht und mit Hilfe eines elektronischen Partikelzählers untersucht. Insgesamt werden mit derselben Ölprobe drei Messungen nach ISO 4406 durchgeführt.
Hierbei zählt man zunächst alle in der Ölprobe enthaltenen Schmutzpartikel, deren Größe 4 µm übersteigen, um sich einen Überblick zu verschaffen. Danach werden alle Partikel, die größer als 6 µm sind, gezählt. Partikel dieser Größe verschmutzen Hydraulikflüssigkeiten derartig, dass der Verschleiß elektroproportionaler Steuerungen deutlich erhöht wird und ihre Funktion beeinträchtigt werden kann. So kann zum Beispiel der Materialabtrag gelappter Bauteile eine reduzierte Leistung der Anlage verursachen. Zuletzt müssen alle Partikel, die über 14 µm groß sind, gezählt werden. Verschmutzungen mit Partikeln dieser Größe können bei hydromechanischen Bauteilen dazu führen, dass Kolben, Steuerscheiben und Schieber klemmen und blockieren.
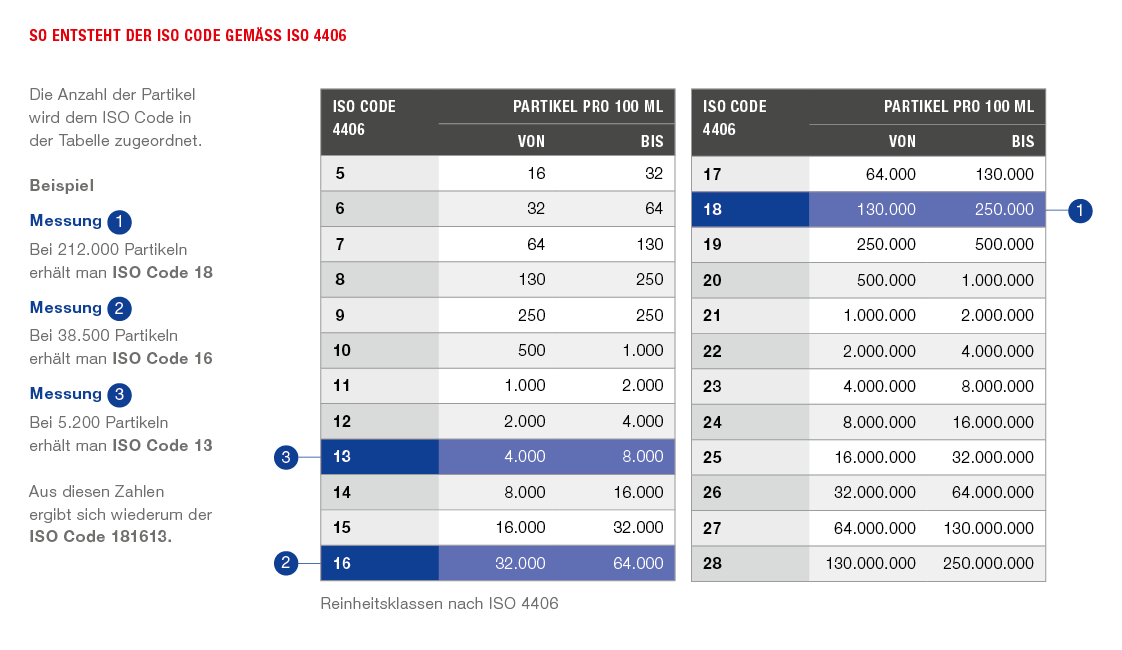
Filtration
Die Filter in Hydrauliksystemen haben die Aufgabe, die Hydraulikflüssigkeit während der Arbeitszyklen permanent zu reinigen. Bei nahezu allen Filtern, die in mobilen Anwendungen eingesetzt werden, sind in den Filtereinsätzen beziehungsweise in den Filtergehäusen Bypass-Ventile verbaut. Diese sollen in Notfällen - zum Beispiel, wenn mehr Hydraulikflüssigkeit durch die Filterfläche im Filterelement abgeleitet wird als eigentlich durchpasst - das Filterelement vor dem Zerbersten schützen. Die jeweiligen Filterarten können optional mit Verschmutzungsanzeigen (Filtersättigung) ausgestattet sein oder nachgerüstet werden. Diese Anzeigen bzw. dieses Zubehör erleichtert Betreibern Wartungs- und Pflegeintervalle, bei denen oft nur die Filtereinsätze getauscht werden müssen, besser beurteilen zu können. Hierbei ist zu beachten, dass sowohl die vorgegebene Filterfeinheit als auch der maximale Volumenstrom mit der Anwendung und den Angaben der Hersteller übereinstimmen müssen.
Filterarten, Einbauorte und Zwecke
SaugfilterundSaugsiebe werden nach Erstinbetriebnahme oder nach Umbauarbeiten zwischen dem Ölbehälter und der Pumpe montiert, um Montagerückstände von der Pumpe fernzuhalten. Die Aufgabe des Ansaugfilters ist es, filtergängige Partikel von der Pumpe fernzuhalten. Achtung: Hersteller empfehlen, bei mobilen Anwendungen in Verbindung mit Kolbenpumpen - bei denen systemtechnisch das Öl der Pumpe zulaufen muss – nach etwa sechs Wochen diese Einheit zu demontieren, sofern eine Fachwerkstatt geprüft und sichergestellt hat, dass sich keine Rückstände im System befinden.
Hochdruckfilterwerden nach der Pumpe und vor der Steuereinheit eingesetzt. Ihre Aufgabe ist es, Schmutzpartikel, die von der der Pumpe selbst erzeugt wurden, auszufiltern und somit die nachfolgenden Aggregate wie die Steuereinheit zu schützen. In diesem Bereich kommen Filter zum Einsatz, deren Filterfeinheit je nach Anforderung und Druck zwischen 7 bis 10 µm liegen.
Einfüll- und Belüftungsfilter in der Hydraulikanlage sind meist am Ölbehälter oder am Rücklauffiltergehäuse befestigt. Ihre Aufgabe ist es, sicherzustellen, dass bei Entnahme von Öl aus dem Tank Außenluft nachgesaugt wird und umgekehrt die Luft über die Filter entweichen kann. Dies soll verhindern, dass ein Vakuum oder Überdruck im Behälter entsteht und diesen beschädigt. Bei der Auswahl der Filter ist zu beachten, dass die verwendeten Filterfeinheiten 10 µm nicht überschreiten und dennoch der maximale Luftaustausch stattfinden kann, um eine Kontamination von außen und damit eine Verschmutzung der Hydraulikflüssigkeit gänzlich auszuschließen. Achtung: In den Dokumentationen der Hersteller werden diese Filter mit anderen Kontrollzyklen behaftet als die Saug-, Druck- und Rücklauffilter. Kontrollzyklen von vier bis sechs Wochen sind keine Seltenheit.
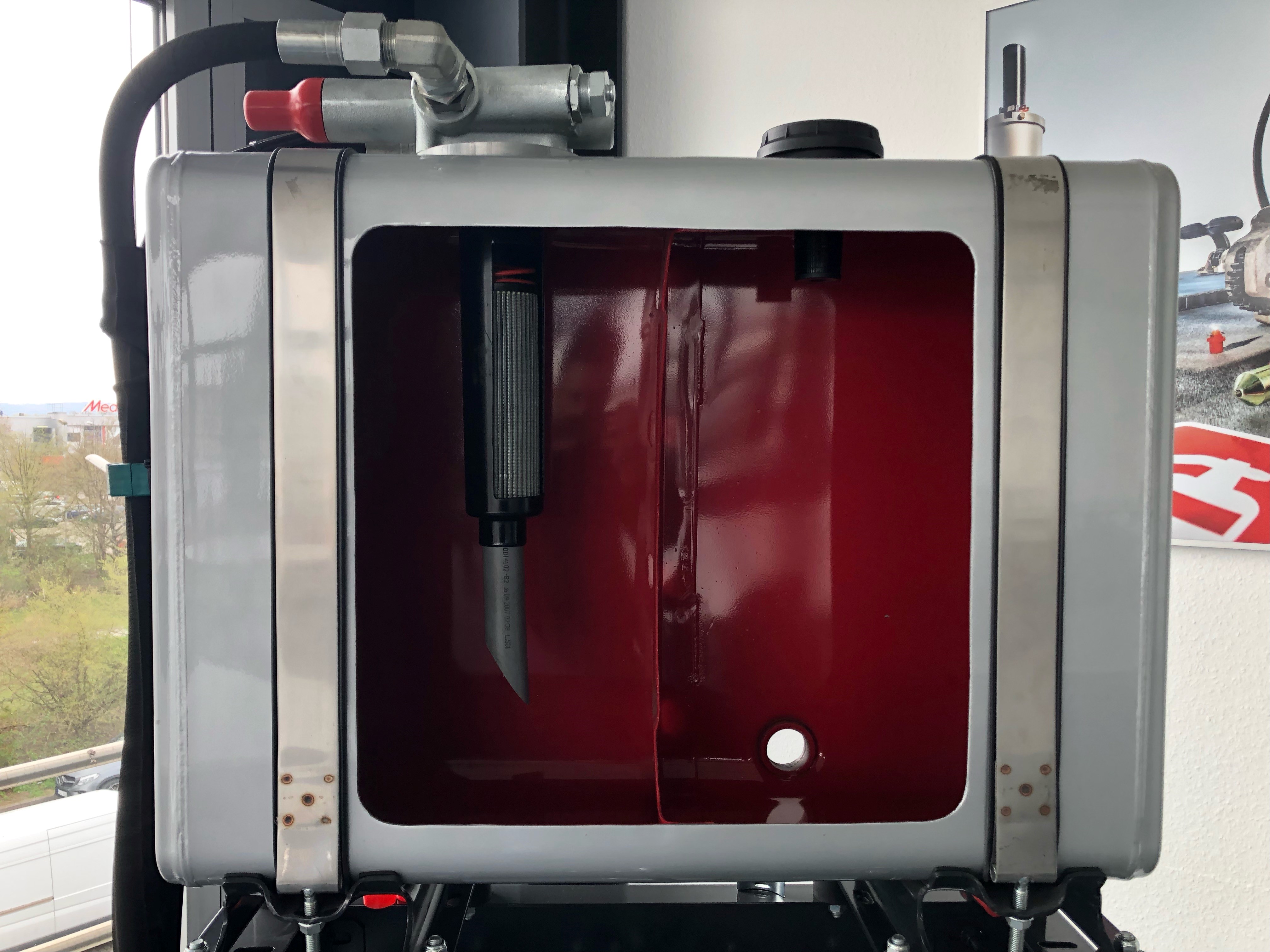
Rücklauffilter werden meist in Ölbehältern montiert. In Sonderanwendungen kann es gelegentlich vorkommen, dass für den Leitungseinbau Rücklaufpatronenfilter nach dem Steuerventil (Ausgang) und dem Ölbehälter (Eingang) montiert sind. Der Rücklauffilter reinigt die Hydraulikflüssigkeit von Schmutzpartikeln, die dann von den Verbrauchern und über die Steuereinheit zum Ölbehälter zurückgeleitet werden. Die Filterfeinheit und der Bypass-Öffnungsdruck der austauschbaren Filtereinsätze sollten beim Austausch mit den Original-Herstellerdaten abgeglichen werden.
Das könnte Sie auch interessieren
Sie haben noch Fragen zum Thema oder möchten uns Feedback geben? Kontaktieren Sie uns einfach über unser Kontaktformular oder über die E-Mail-Adresse hydraulikmagazin@winkler.de. Wir freuen uns auf Ihren Input!
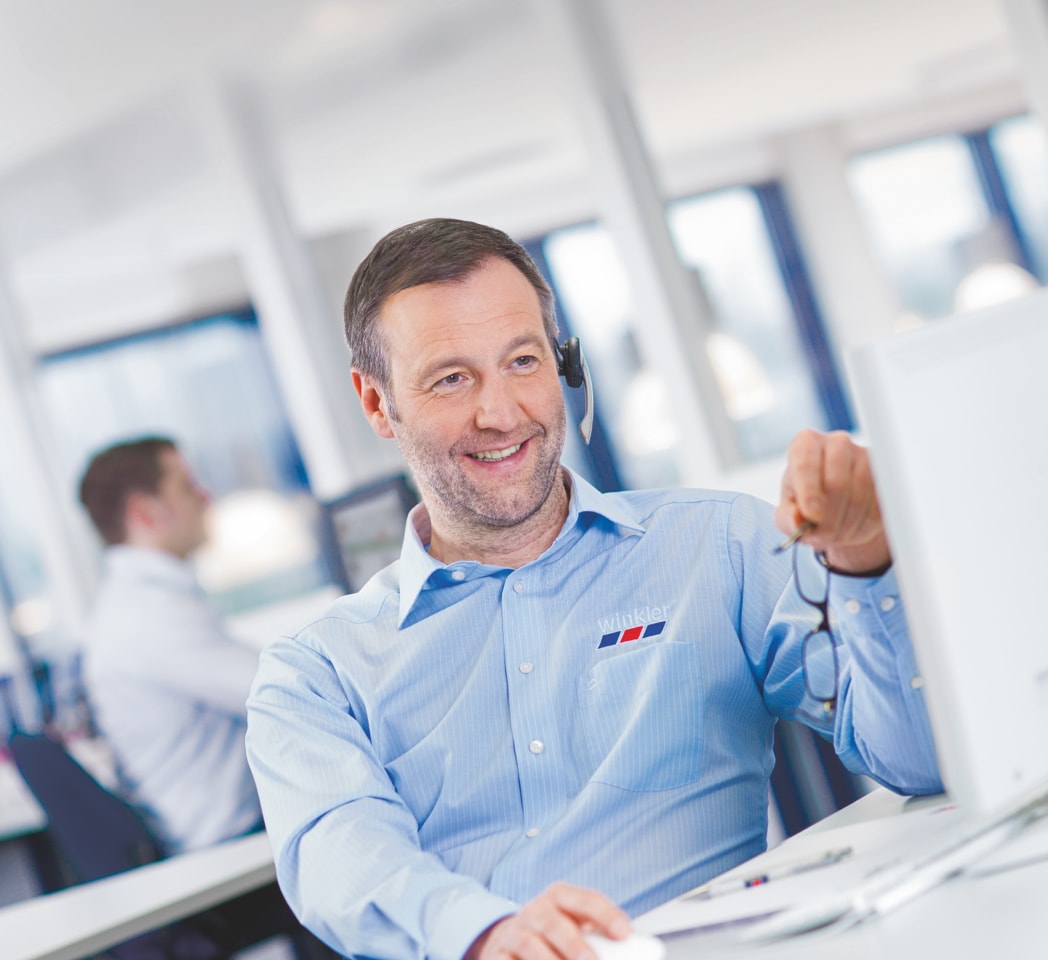